|
 |
1.ポカミスの種類と発生メカニズム
1)不良をつくる5つの要素
2)不良のワースト10は?
- 加工忘れ
- 加工ミス
- ワークセットミス
- 欠品
- 異品混入
- ワーク違い
- 誤動作
- 調整ミス
- 段取りミス
- 治具不良
3)ミスの種類
不良の原因のほとんどが人のミスです。
- ウッカリミス
- ウッカリしていたり、忘れたりして起きるミス。
- 遮断機の降ろし忘れ。(事前確認、定期確認、呼称確認)
- ガッテンミス
- 気が早かったり、勘違いが引き起こすミス。
- ノークラの車で、クラッチのつもりでブレーキを踏む。(打合せ、事前確認、標準作業)
- チラミス
- 見落としたり、チラッと見ただけで間違えるミス。
- 千円札と五千円札の見間違え。(打合せ、注意)
- アマミス
- 知らない仕事や生半可な仕事ナド、アマチュア的なやり方で犯すミス。
- うろ覚えでの作業で失敗。(熟練、標準作業)
- カッテミス
- この程度ならかまわないと、勝手に決め込んでルールを無視するミス。
- 電車のキセル、みんなで渡る赤信号。(基礎教育、躾、習慣)
- ポカミス
- 自分でも、どうしてこうなったかわからないような、ポカーッとして発生するミス。
- 赤信号なのにトコトコ歩いて行く。(注意、規律、標準作業)
- ニブミス
- 判断の遅れにより、反応や動作がニブッてしまい発生したミス。
- 初心者マークをつけた車のブレーキ踏み遅れ。(熟練、標準作業)
- パナシミス
- 適切な指示も、標準作業もなく、作業者にまかせっパナシで起こるミス。
- 管理、統制のない現場は不良の宝庫。(標準作業、作業指示)
- アレミス
- 予期した動きをしないで、「アレ?」と思わせるミス。
- 機械の誤動作。(トータルPM、標準作業)
- ワザミス
2.まず、ポカミスクレームの再発防止を
1)暫定対策のままで終わるな
- 再発防止書と現状のちがい。
- マーキングは流出防止の暫定対策であり、効果時間は20分間。
2)DRを上手に活用する
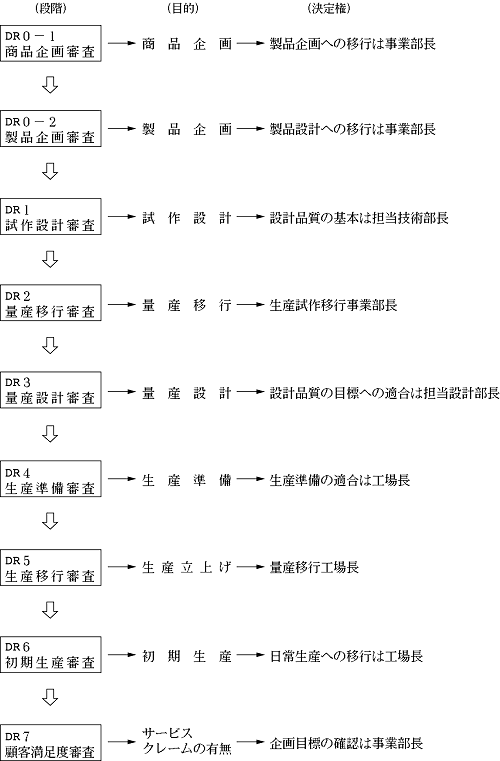
図1 A社のDR内容
3.ポカミス防止手順
- 手順1.ポカミスヒヤリマップの作成
- 選ぶ、さがす、仮置き、製品不良、設備不良、人間不良、をチェック。
- 手順2.マニュアルを作らない。現場に貼らないオペレーターの責任にしない。
- マニュアルを作って終わる管理者。
- マニュアルを作ると不良がなくなると勘違いする管理者。
- 作業手順書は、作業台の上に貼らなければいけないと思い込んでいる管理者。
- 不良が発生するとオペレーターのせいにする管理者。
- 手順3.サイクルタイムの定義付け
- 時間のバラツキ。ものつくりにリズムがあるかどうか、現場を見る。
- リズムが崩れるとポカミスが発生する環境になる。
- 手順4.工程設計の見直し
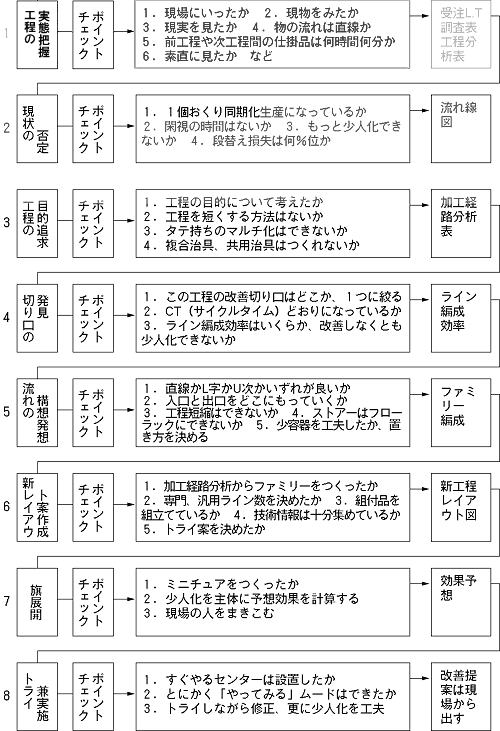
図2 1個造り用工程ばらし手順
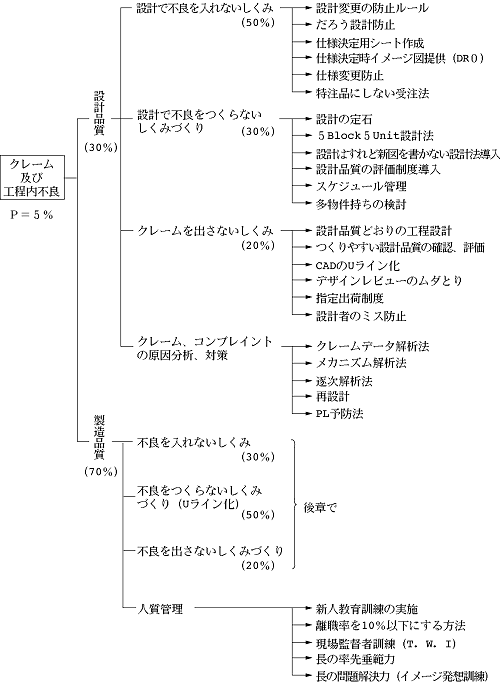
図3 設計不良を入れない、造らない、出さないしくみづくり
- 手順5.4Standerd設計
- 仮置き防止のため、物の置き方4Sを徹底する。
- 物の置き場所を決める。
- 何を置くか決める。
- 置く量を決める。
- 置く順序を決める。
- 定位置停止ルールを決める。
- 手順6.ポカミス対策はメカで行う
- 治具化。
- スイッチ等の信号発信。
- 設備の回路と(2)を接続。
- 前工程の設備回路と3.を接続しAND回路を組む。
- 手順7.工場からペンを取り、情報をつなぐ
- 記入時、ものから手や目が離れる。
4.ポカミス1つなくせない管理者は現場から去れ
管理者の条件
- 現場を見て正常と異常の判断ができる。
- 異常を正常に戻す処置をすぐ実施できる。
- オペレーターの健康状態を常に把握している。
- 部下育成能力がある。
- 自己革新能力がある。
- 製造業としてのあるべき姿を常にイメージしている。
- 日常業務と改善業務、各20項目が常に貯金されている。
- 「オペレーターはラインを止めよ。管理・監督者はラインを止めるな」の意味が理解できる。
- 部下のミスは管理者である自分の責任である。
- 事後処理から事前管理のポカミス対策をする。
|