|
 |
1.技術の進歩と保全(メンテナンス)の歴史
保全の歴史は、技術発展歴史に見るように、西暦紀元前(BC)4000〜400年頃に始まり、BC3000年頃のエジプト、大ピラミッド時代にすでにその萌芽がみられ、あさらに中国では、紀元後(AD)214年に行われた万里の長城の増改築が行われている。
アルキメデスがポンプを開発したのがAD200年、以後技術の進歩と機械の改善の歴史は、滔々として現在に至っているといえるだろう。
中世においても、618〜907年の中国の唐時代におけるわが国の遣唐使船、近世においては1490〜1500年にかけて、レオナルド・ダ・ヴィンチによる中ぐり盤、圧延機、水力タービン、渦巻きポンプなどの考案など枚挙にいとまがない。
幕末の1853年には、江川太郎左右衛門が、下田に反射炉を設置(翌年韮山に移す)したのである。
18967年日本は明治維新となり、新しい時代が始まった。
文明開化のスタートを切ったのは鉄道であった。鉄道は1869年(明治2年)11月10日鉄道建設の廟儀決定が行われ、1872年には小田原電気鉄道が開通した。また一般産業においても、1897年八幡製鉄所発足、1912年田熊常吉による田熊式汽缶開発、そして1917年本田光太郎KS磁石鋼開発などがある。1923年には東京丸ビルが建築された。
技術の進歩は文化面でも勢いづいていた。
1925年東京放送局開設、1928年高柳健太郎日本最初のテレビ実験、1939年桜田らが「ビニロン」を発見したのである。しかし技術は、1945年原子力爆弾の最初の使用(広島・長崎)のように明るい面だけをもたらしたのではなかった。
技術の開発の歴史は古代から現代に至るまで続いているわけではあるが、これと並行して保全の歴史も共存の形で発達を遂げ、今日まで至っているのである。西洋の近代技術ばかりではない。
いまから1300年も前の飛鳥時代に建立された法隆寺や薬師寺などは、宮大工といわれる棟梁等によって代々引き継がれ、保全が行われて今日に至っているのである。
船における技術と保全の関係をみてみよう。
遣唐使船から、幕末の或臨丸などを経て、明治元年(1868年)以降、乗組員の定数および船主と乗組員の関係は、西洋形商船船長運転手免状規則(明治9年/1877年制定、明治12年・1880年施行)、西洋形商船海員雇入・雇止規則(明治12年/1880年制定・施行)を経て、明治29年(1898年)からは4年間に全船舶を対象にした船舶検査法、船舶職員法、船員法、船舶法が制定された。
そして本格的な船舶の保全要員育成のための教育機関として商船学校が設立されている。筆者の母校の設立も明治30年(1897年)であり、いまから107年前のことである。
また、明治41年(1908年)に建造された日本最初の1万トン級の豪華客船、天洋丸は、その高い造船技術とともに太平洋航路の白眉として内外の注目を集めた。
1904年日露戦争の日本海海戦時「敵艦見ゆ」の信号を発した信濃丸(7000トン、レシプロ蒸気エンジン)が蟹工母船を経て、1945年以降復員船として専門の資格を持ったメンテナンス・エンジニアが運行に当たったからである。
1783年11月21日、フランスのモンゴルフィエ兄弟が熱気球に初飛行した。1903年にはアメリカのライト兄弟がグライダーにガソリンエンジンをつけて飛行に成功。1929年にはドイツのツェッペリン飛行船がゆらりと世界一周に出かけ、航空機自体の開発も進められ、プロペラ機からジェット機へと進歩を遂げてきた。
航空機の保全方式は、現在でも一般生産工場で用いられている、いわゆる時間基準保全(Time Based Maintenance)といわれるもので、機器ごとに運転条件や環境条件などにより、特定の周期で実施する大検査で、2〜4年に1回程度行われる。
このように一定時間ごとに行われる検査なので、時間保全基準と呼んでいる。会社によってはこれを定期修理(定修)といっているところもあるが、本当は定期検査(定検)なのである。
航空機の場合は、これを稼働時間基準方式(Hard Time Process)と呼び、一定時間稼働したら分解点検整備(Periodic Over-haul)または、機器・部品の交換(Replacement)を実施している。
現在、航空機でも全体の6%程度は、この時間基準保全が実施され、耐用寿命の延長が図られている。
つぎに、状態基準保全(Condition Based Maintenance)は、定まった修理間隔を設けず、機器の診断技術により、機器の劣化や故障の前兆となるような不具合の有無を発見し、必要な時期に必要な保全を実施する方式である。
航空機の場合1960年頃より機能基準方式(On Condition Process)と呼び、機体、系統、機器、部品別に機能劣化の限度を定め、この限度に到達したら分解整備や交換整備を実施している場合が全体の5%を占めている。
また、機能監視保全(Condition Monitoring Maintenance)機器の系統またはユニットについて、その機器状態を常時監視して、系統またはユニットを構成する機器や部品の故障発生以前に示す兆候を発見し、故障発見を防止する処置をとるような保全を状態監視保全という。
航空機の場合は1960年代後半に航空機の設計段階から信頼性を考慮した信頼性管理計画(Reliability Control Program)を確立するため、今までに経験したあらゆるユニットや機器、部品の故障データを集めて分析した。
それと同時に世界各国の航空会社に対して、これらにどの程度の信頼性を達成するための信頼性設計に取り組むとともに、信頼性評価試験や故障解析データ処理による信頼性保証体制を確立した。
さらに、これらに対応する保全方式が研究開発され、新たに機能監視方式(Condition Monitoring)が採用された。航空機の運行や整備を通じて発見された故障情報を集め、監視(Monitor)し、解析(Analysis)、統計的処理等を行って、故障の原因を追究し、故障原因を排除する改善対策の立案実施を行うとともに、保全方法の改定を実施して現在に至っている。この保全方式の場合、全体の89%を占めている。
筆者が航空機の例を少し詳しく述べたのは、生産工場における要素部品・機器・系統の保全の信頼性管理体系は、一般の生産機器の場合、航空機や船舶などの乗り物の保全(整備)に比較して30余年の遅れを感じているためである。
航空機などの保全は、機器の故障が万が一にも発生すると、人命にかかわる仕事であり、当然、国で認定した整備の資格がなければその仕事を遂行することはできない。生産工場でよくある機器の“チョコ停”などというような、悠長なことは言っていられない。機器の故障=(イコール)人命事故という緊迫感が保全(整備)に対する要員の心構えの違い、意識の差となっているように見受けられる。
ところがこのような安全性がゆらぎはじめた。航空機、自動車、原子力発電の事故の多発は何が原因だろうか。
2.何故、事故は起こるか? ─データがないことが再発をゆるす─
製造物責任法(PL法)は、平成6年6月24日の公布閣議を経て、平成6年法律第85号として平成6年7月1日に公布され、平成7年7月1日から施行された。この法律 は、これまでの製品関連事故についての損害賠償責任原則を、「過失」から「欠陥」に転換するものである。
製造物責任法の条文の解釈による「製造」とは、製品の設計、加工、検査表示を含む一連の行為として位置づけられ、一般には、「原材料に手を加えて新たな物品を作り出すこと、生産よりは狭い概念で、いわゆる第二次産業にかかわる生産行為を指し、一次産品の産出、サービスの提供には用いられない」を表わしている。
また「加工」とは、「動産を材料としてこれに工作を加え、その本質は保持させつつ新しい属性を付加し、価値を加えること」である。
本法では、欠陥概念の明確化の要請と争点の拡散(被害者の立証負担の増加)防止の要請との調整の」観点から、共通性、重要性、両当事者に中立的な表現ということを念頭に、欠陥判断に際して総合的に勘案されるべき考慮事情として、「当該製造物の特性」、「通常予見される使用形態」および「その製造業者等が当該製造物を引き渡した時期」の三つを示している。
生産工場にあっては、いわゆるPLP(Product diability Prevention)といわれる製造物責任予防対策が必要である。しかしながら加工現場においては、マニュアル通りにゆかない事柄が多い。そして不良品や欠陥が出る。なぜか?
人間が各人肌の色や顔形が違うように、あらゆる物質は千差万別であり、理論的にはこの世の中に同一のものは一つもない。技術者はこのことをよく理解しなければならない。そのために相似のものを同一と見なすために、それぞれの範囲や基準を設けた統計的手法や、確率を使った品質管理の手法が必要になってくるのである。
生産工場で加工された製品が、工場出荷後、使用現場において製品(機器)が故障や事故をおこした場合の、保全部署における製品使用時の欠陥の見分け方が非常に重要であり、そのデータの集積が再発を防止するのである。
先に述べたPL法は、第二次産業にかかわる生産行為を指しているが、製品(機器)の故障や事故を解析、分析する過程において、素材産業の金属の組織や、流体の成分などが少なからず缶よしていることを、数多く経験した。
よく理論と実際という言葉が使われるが、学校教育の逆発送とでもいうか、実際の現場、現物、現実の問題点を具体的に解析、解決する過程において、事実にもとづいた逆の面からのアプローチにより、理論に結びつけることが肝心である。
現場で実力を虚心に見ることにより、自然の摂理の偉大さと、自然科学の中の機械、電気、化学、物理、数学、材料、力学、また、その境界領域の本質を身につけることができ、製品(機器)使用現場におけるトラブル発生時の判断力を養ううえで、役立つことと思う。
製品使用時における欠陥を見分ける場合、まずそフ時点での、ものの診方、考え方を理解してもらうと同時に、機器とはどんなものか、そして機器を使用する際は、すでにはじめから80%くらいの欠陥を内蔵していることを肝に銘じて、その解析にあたってもらいたいために、あえて申し述べた次第である。機器の信頼性の要点は、破損物件の回収による解析と対策が基本である。せっかくの故障見本を汚いもののように廃棄していないか。それを保存するかデータ化する<想い>がなければ事故は何回でも起こるのも当然である。
3.ものの診方、考え方を変える ─油はなぜ黒くなる─
車のエンジン油を交換するとき、古い油は真っ黒になっていることは、ドライバーならば誰もが知っていることである。「なぜ黒くなると思うか」と問われると「それはエンジンの熱で油が焼けるからだ」10人が10人ともそう答えるだろう。「本当にそうなのか?」ということは別にして、この答えは大変わかりやすい。燃料油が燃えると「すす」が出る。だから黒くなるというわけだ。
ところが、燃えるはずのない油圧機器の作動油も古くなると黒くなるのである。われわれの日常の感覚では、油圧系統で油の燃える部分はない。しかし油が黒くなるのは作動油だけではない。潤滑油(ベアリングの潤滑油、モータの潤滑油、空気圧縮機の潤滑油など)もそうである。そこであらためて「油はなぜ黒くなるのか」という問いかけとなる。
さて、われわれが直接見たり触れたりすることのできない「ミクロの世界」、「マクロの世界」では、われわれの日常の常識とは、大変かけ離れた出来事が起こるのであるが、この作動油の黒化現象については専門家の見解はこうである。わずらわしい計算式は横において、大筋は「油中の微小な気泡が圧縮されて、ミクロ的な部分で高熱(数百〜千度)が発生し油が燃えるからだ」というわけである。圧縮機だけで着火するディーゼルエンジンのことを思うと、「なるほど」と素人にも納得できる。
このように、われわれは(専門家も含めて)油が黒くなる原因は、「熱による油の燃焼が原因」と一応納得している。しかしこの原因説については、深く考えれば考えるほど、ひと筋縄ではいかないことがわかってくる。専門家はこれを「バラツキ因子」として、それがなんであるかを模索している。
先に述べたように、分子、原子の世界や宇宙の天体現象のように、ミクロの話が横道にそれたようであるが、これは決して横道ではない。ここで、あらためて油の黒化現象について考えてみる。その原因を探るには、もろもろの黒化現象について、その共通点を取りあげ、それについて考察するのが近道である。すると油(炭化水素)が存在する環境で、金属の摩耗が継続点に起こっていることである。「熱」は影響因子の一つではあるが、決して共通点とはいえない。このような環境で何が起こるか。金属が摩耗するということは、当然のことながら裸の金属表面の露出が継続的に起こっていると考えてよい。また摩耗面には、外部よりの塵埃の混入はつきものである。そしてその半分は砂ぼこりである。この砂が摩耗面のすきまに噛み込まれて粉砕したとき現われる表面は、十分触媒になり得るエネルギーを持つことは、前に述べたとおりである。
ここで見逃してはならないのは、油圧ポンプに生じるキャビテーションエロージョンである。これも歴然とした摩耗現象である。キャビテーションとは、液体の激しい乱流によって発生する局部的な負圧によって、液体中の容存空気が気泡となり微小な空洞ができる現象のことで、この空洞はもちろん、瞬時に発生して瞬時に消えるわけであるが、これが潰れるときに液体が爆発的な速度でぶつかり合い、おそろしく大きい圧力となる。この圧力に触れた固体表面は無数のクレーター状の摩耗痕を残す。これをキャビテーションエロージョンという。このことからわかるように、キャビテーシ
ョンは金属表面を裸にして活性化するとともに、自身の爆発的な圧力によって油を分解、重合させる作用がある。
油が黒くなるのは、裸の金属表面のきわめて大きいエネルギー(活性)がかかわっていることが、その根底にあるのである。このことは当然油の劣化、変質にもかかわっている。
油が黒くなるのはなぜか。「そんなことはどうでもよいことだ。われわれの知りたいのは黒くなった油が、あるいは劣化変質した油が、機器にどのような悪影響を及ぼすのかということなのだ」という声が聞こえてくるような気がする。もちろんそのとおりである。たしかに油が黒くなろうが赤くなろうが、その変化が機器に及ぼす影響さえわかれば事たりるのであるから。
筆者がここで述べたことは、“ものの考え方はかくあるべし”ということを、「油はなぜ黒くなる?」という問いかけを通していいたかったわけである。ありふれた日常の出来事も、原子・分子レベルのミクロの作用がその根底にあって、マクロの現象、すなわちわれわれになじみ深い出来事が起こるわけである。前に述べたように原子・分子レベル現象はわれわれの常識をはるかに超えているものである。故障の解析にあたっては、マクロで現象を観察し、その根底にあるミクロの現象を頭において考察することが大切である、ということである。エローションとコロージョンが複合化した場合、お手上げにならないためにも、正しく、現象を把握する眼を頭を、日頃からきたえることが事故でふせぐ基本にならなくてはならない。
4.欠陥と故障を解析する
同じ現場の同型のNC旋盤が、1カ月も満たない間に相前後して故障を起こした。しかもどちらも同じ主軸のベアリングの損傷である。ところが、一方の機械は立ち上がり2年であるが、他方の機械は立ち上がりわずか2カ月にすぎない。先に故障を起こしたのは、立ち上がり2年の機械であったが。それにしても、普通ならばわずか2年で主軸のベアリングが壊れることはまずない。立ち上がり2カ月の機械にいたっては論外である。当然のことながら、ユーザーは工作機械メーカーに抗議し調査を依頼し た。ベルトの締め付けが適切でないのではないか、機械の据え付けが悪く異常振動が発生し、軸受の破損につながったのではないかということが疑問点として取りあげられた。はたしてこの場合はどうであろうか。
一般に機器・システムの故障は、80%以上が製造者側の設計、製造にかかわるもので、使用者側に原因があるものは20%といわれている(図1)。
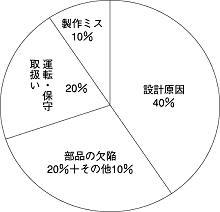 |
図1 故障原因構成比 |
そして故障の発生状態にある一つの傾向のあることが知られている。それはどういうことかというと、立ち上がった当初に比較的故障が多発するが、その後次第に安定な状態となり、しばらくは安定状態が続いたのち再び故障が増え始めるというのである。このような傾向を図で表わすと図2のようになり、あたかも西洋浴槽の断面に似ているので、保全技術者の間ではバス・タブ曲線といわれている。製造者側の責任にかかわる事故はおおむねこの初期段階に発生する。この段階を初期故障期間といっている。初期故障とは設計、製造の過程での誤りや欠陥が原因で起こる故障のことをいう。したがって一般的には、機器・システムがメーカーからユーザーに手渡される前に、この初期故障期間がすぎていることがたてまえである。メーカーは出荷後の故障率を下げるために、この期間にならし運転、環境過負荷などの信頼性試験を行うわけである。そして納入後しばらくの間安定な状態が続く。
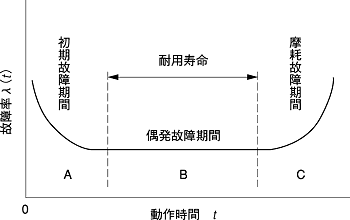 |
図2 故障率曲線 |
この安定状態の段階では、故障の発生は少なく、一般に耐用寿命期間といわれているが、作業者の操作ミス、使用環境の悪化のような偶発的な故障はこの期間でも避けて通ることはできない。そこで、この段階を偶発故障期間と呼んでいる。偶発故障とは、設計の段階では予測されない出来事、たとえば使用環境の悪化、作業者のミスなど使用上の欠陥が原因となる故障をいう。この期間といえでも摩耗、疲労は徐々に進んでいることはもちろんである。だからこそ、この段階での予知保全が重要で、これが適切に行われるか否かは、機器・システムの寿命に大きな影響を及ぼすことになる。そして最終的には摩耗、疲労により再び故障が多発する傾向が現われる。この段階が疲労摩耗故障期間といわれている。
さて話をもとに戻そう。今回のベアリングの破損はあまりにも早い時期に起こった。しかも2台とも同じ故障である。ユーザー側は、初期故障期間の出来事で、製造者側の責任にかかわる機器の欠陥であると主張した。製造者側はこのような事故は過去に例がない。これは偶発故障で当方には責任がないと主張するだけである。とりあえず軸受の取りかえを行ったが、それ以上のアクションはない。あとは「修理費を払え」。「払わない」という交渉があるだけである。破損したベアリングのメーカーにこの破損について調査を依頼したところ、このような破損はいままでまったく経験がないので、原因はわからないという回答である。
ここでやらねばならぬことは、とりあえず故障部品を交換することも必要であるが、大切なことは、徹底した故障解析である。ところがユーザー、メーカー双方とも前記のような言い分を繰り返すだけで、客観的な立場で故障解析をやろうとする姿勢がない。このような事故の場合の故障解析は、メーカーとユーザーが情報を提供し合うことが必要であるのであるが、おたがいに経済的な利害がかかわっているので、自分に不利になるような事柄には触れたくないという意識が強く働くので、なかなか原因をつき止めることができない。
さてこの場合、設計、製造上の欠陥が原因の初期故障なのか、作業上の欠陥が原因の偶発故障なのか、故障解析の結果、ユーザー側の加工条件設定の欠陥による偶発故障であることがわかった。その後、この2台の機械では、偶発故障は起こっていない。
もう一例、3台の同じ型の工作機械の同じ部分が、たて続けに破損した。このような場合に、誰もがその壊れた部分に欠陥があるのではないかと考える。それは一応もっともなことである。しかしちょっと考えねばならないことは、この謔、な場合壊れた部分、部品にだけに気が取られがちとなることである。大切なことは、壊れた部分、部品の調査もさることながら、機械あるいはシステム全般を見直すことがさらに重要である。破損部分の欠陥が直接故障原因となっている場合はむしろ少ない。この事例の場合は、本文で述べたようにゼネバアームの異常振動が原因であった。そして、その振動の原因はローラ内外での異物の噛込みによるころがり振動と、慣性モーメント が大きいことがわかった。このような異物の混入や慣性モーメントの問題、材料選択の欠陥は機械の構造上の問題であって、設計段階ではおそらくこのことは予想していなかったに違いない、いわば設計ミスであり、機械構造の欠陥である。
機械のある部分が壊れる。とりあえず壊れた部分を取りかえる。これは誰もがやる対応である。そしてしばらく使って異常がなければ、ずるずるとそのまますごしてしまい、破損の原因が究明されないまま忘れ去られてしまうことが多い。たとえ偶発故障であっても、それなりの原因がある。その原因解明し、欠陥と故障との因果関係を記録として蓄積し、故障解析の資料として将来に資することこそ、真の故障対策といえよう。
物づくりに信念と自負を持つ現場のエンジニアなら、メンテナンス・マネジメントとして故障、欠陥データの集積が必須である。このことが、中国やアメリカの物づくりとの差異を生み出し、我国の製品優位性につながると信じる。(逆に中国やアメリカがそのことに早く気づき、我国が放置している場合は、日本沈没は一段と早まるであろう。)
我国の現場のエンジニアには、真摯に物づくりに携わる人々が大勢いる。彼らを大きく育てないのはマネージャーの責任である。工場のマネジメントが重大なゆえんがここにあると思う。我々はもうすぐ逝くが、後に残る我国の物づくりの将来を思うが故に一筆したためたしだいである。
|