|
 |
S社はモーター業界のシェア11%を持つ大手である。ところが価格競争の結果、赤字企業に転落、対策として私共に工程ばらし、工場ばらしによる少人化ラインづくりの相談をうけたので、同労者、Tチーフコンサルタントが担当、その足跡を工場管理誌、Vol.43.No.7で発表した事例である。内容的には工程ばらしだったので、本マニュアルでは、専用に近いモーター工場の場合の工場レイアウト案を追加した内容である。
1.S社モーター工場の流れ線図を入れた図1−1工場レイアウトを見てほしい。
本来は、運搬のムダを積卸し−積込みを考慮した上下運搬の難易度係数を算出して評価したかったのであるが整理に時間がかかるのでやめ、「整流化、流れづくり」に主体をおき工程ばらしによる少人化ラインづくりに集中した。
2.S電機5つのムダ
早速、工場診断を実施したところ、次の5つのムダが明らかになった。
(1)レイアウトのムダ、(2)運搬のムダ、(3)仕掛り在庫のムダ、(4)手待ちのムダ、(5)不良のムダ図1−1を見ていただきたい。改善前のレイアウト図である。図中の点線は、運搬経路を示している。
(1)のレイアウトのムダの発生原因は、
- 通路が国道、県道、市道というようにレイアウトされていない。国道を先にレイアウトしていない。
- 加工、組付け、組立、梱包と工程順にレイアウトされていない。ジグザグになっている。
結果として、(2)の運搬のムダが発生している。運搬距離はPSCモーターだけでも145mである。また運搬距離が長いため、小ロットの運搬をせず、できる限り大ロットで運搬しようとする。工程間には(3)の仕掛り在庫が山積する結果になっている。
仕掛り在庫は、半完成品だけで約25日分もあった。またラインは、直線コンベヤーラインを基本としているため、コンベヤーライン特有の助け合いができないムダおよび取り置きのムダ、ならびにH.T(手扱い作業)100%のムダが発生していた。これは結果として、(4)の手待ちのムダになる。
(5)の不良のムダは、工程間仕掛りが多いため箱の積み重ねや移し替え時に発生するキズ、変形不良が50%近く出ていたのである。
諸悪の根源はレイアウトのまずさにある。
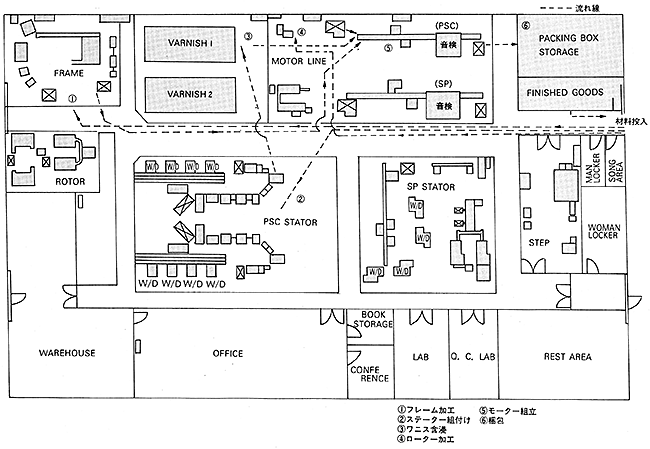 |
図1−1 S社モーター工場の流れ線図(PSCモーター改善前) |
3.改善方針
工場診断後、5つのムダをS副社長をはじめ現場幹部に説明、結論として工程ばらしからスタートするように提案した。
韓国では工程ばらしのことを工程再編成技術という。私の著書、参考文献1のほんやくであるから、内容的にはまったく同じである〔参考文献1〕の15頁のとおり。
全工場のレイアウト変更は困難であるから、工程ばらしに集中した。工程ばらしの技術を習得するためには若干のIE的知識がいるので、幹部との思想統一から入ることにした。
- 改善の思想統一
改善を成功させる準備として、考え方の統一がいる。これを思想統一という。思想が統一されていれば、方法、手段の発想が違っても調整が可能だからである。そうしないと改善が途中でストップしてしまうからである。
三星エマソンでは、現場オペレータにも改善イメージを持ってもらうため、図1−2のようなポスターをつくって掲示してもらった。
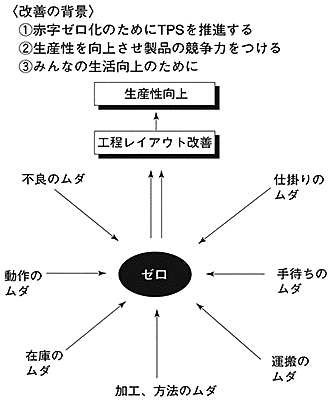 |
図1−2 改善の思想統一用ポスター |
- 改善プロセスを決める
思想が統一されたならば、改善のプロセスを決める。図1−3がそれである。工場診断後、オペレーター全員を集め、TPS7つのムダについてワークショップを実施、2月よりキックオフすることを宣言した。
順序としては、まず、工程、レイアウトの変更、中味は、加工→組付け→組立と、モジュール別に工程をばらすことにした。
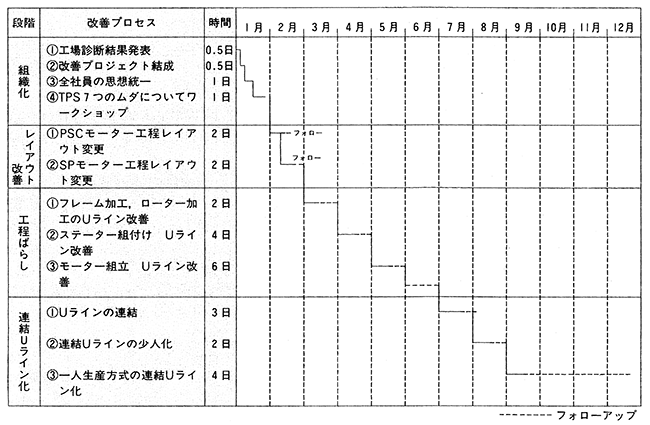 |
図1−3 改善プロセス 主テーマ「ONE PEACE FLLOW」 |
- 改善プロジェクトチームの編成
1年という短期間で成果を出すには、プロジェクトチームをつくり、改善を専任化しないと成功しない。
S社では、崔副社長(写真1−1)をリーダーに合理化、生産技術、現場幹部から合計7名のメンバーが選ばれ、プロジェクトチームを編成した。当然のことであるが、彼らの日常業務は「改善」が専業になる。
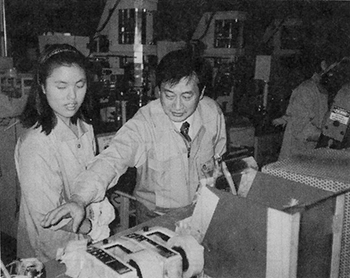 |
写真1−1 崔副社長、自ら取り置きの現場指導 |
- 工程ばらしの内容
全面的な工場レイアウト改善は金がかかるので1部のみにした。
工場レイアウト設計は、水路設計に似ている。設計が悪いと、水の流れ(モノと情報の流れ)が悪くなり、ごみが溜ったり(不良品の停滞)、洪水(運搬の輻輳、停滞、在庫)にもなる。
もう一度、図1−1をみてほしい。
改善点は、次の4項目になると思う。
(1) 国道に相当するメイン通路を中央にとる。
(2) 工場の入口から工程順に製品グループ別に流れをつくる。
本例の場合はPSC、SPタイプ別の2本ラインになる。
(3) 将来、連結Uラインがやりやすいように当面小Uラインをつくる。
(4) QC室と作業トレーニング室は、現場に設置する。
改善後のレイアウトは図1−4である。 で示したところがレイアウト変更場所である。効果は表1−1のとおり。PSCラインでは、スペースで90.5m2の縮小、運搬距離では47m短縮。合計210.2m2スペースが空き、118m運搬距離が短縮した。
以上が工程ばらしの概要である。
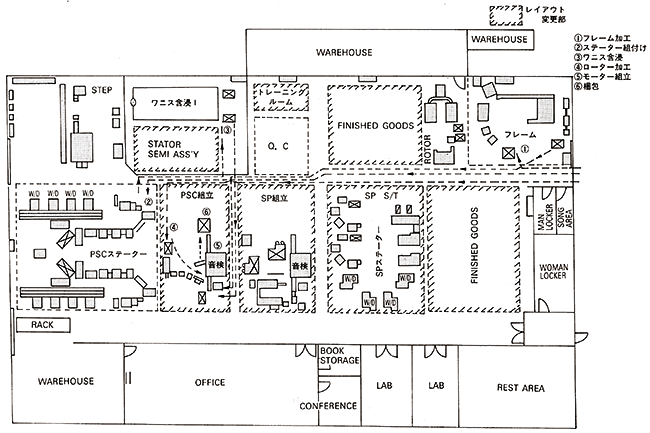 |
図1−4 S社モーター工場の改善後レイアウト |
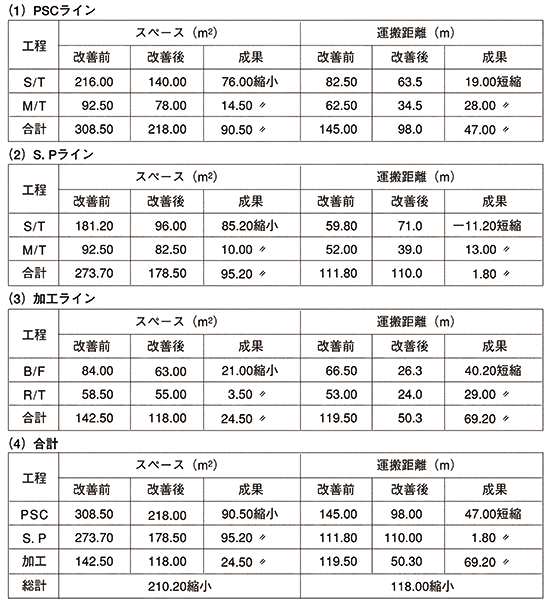 |
表1−1 レイアウト改善成果 |
改善提案の目的は、(1)現場で実際に作業する人たちの改善意識の向上、(2)小さなムダ取り実践である。
改善提案制度を実施したところ、人員96名に対し、1カ月で283件の提案が出てきた。1人当たり約3件の提案になる。これを作業者、組長、班長、プロジェクトチームのメンバーで審査し、即実践する。同時に最多提案賞、最優秀改善賞を決める。この制度は現在も継続中であり、3年で1,000件を超えている。
S社は韓国企業の中で、最も社員教育に熱心である。たとえば、日本の工場でのモノづくりの現場実習教育に、すでに1,000名以上の社員を派遣している。女性社員も社内教育で2カ月に1回の割合で繰り返し教育を受けている。教育により人質の向上は日本以上かも知れない。
工場レイアウト改善は未完であるが工程ばらしには成功した。
第1工程のフレーム加工からスタートすることにした。図1−5は改善前のラインである。第1のムダはワンマン、ワンマシンによる手待ちのムダ、第2は大ロット生産による中間仕掛品のムダである。正味加工時間21秒に対し、L.Tは約3時間と長い。工程分断による仕掛り品の山積が原因である。
改善手順は、
- 手順1:まず、H.T(手扱い時間)とM.T(自動加工時間)を測定する。M.Tはバラツキがないので1回の測定でOK。
また、H.Tは機械への取り付けと取り外しであるから3回程度の測定でよい。
- 手順2:測定の結果、約50%が手待ちと判明〔算出方法については参考文献1)を参照〕。
- 手順3:フレームの1個流し設計
図1−5は改善前のレイアウトである。稼働時間は16時間。1日の必要数は6,000個。C.Tは9.6秒になる。手順2での測定結果はΣHTは21秒。必要人員は2.18人となる。改善前は4名であるから、1.82人工少人化ができる計算になる。
ただし、人間の場合は小数点以下の端数はとれないので0.18人工分のH.Tをとり(理論値1.82人工+改善によるH.T短縮0.18人工=2人工)、2名少人化したのが図1−6である。1個流し用シューターを2カ所に取り付け、取り置きのムダをそれぞれ1回ずつとった。
結果は、目標通り2名少人化に成功(写真1−2参照)。モノの流れも、工程間に仕掛りを持たず、1個流し化に成功した。また、オペレーターは1人2工程持ちの多能工となり、単純作業から解放されている。
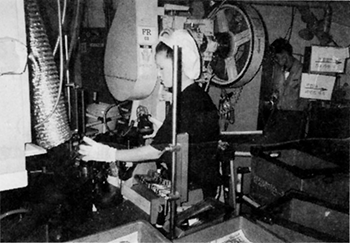 |
写真1−2 フレーム加工(改善後)の2人ライン |
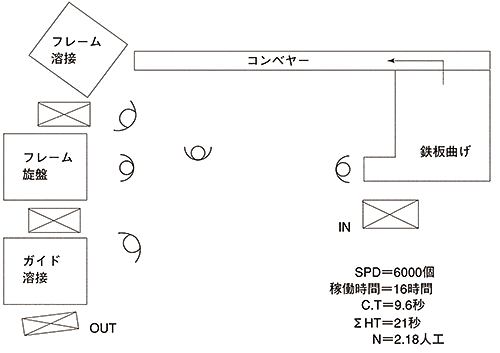 |
図1−5 フレーム加工(改善前) |
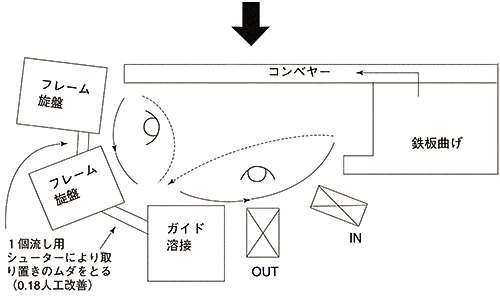 |
図1−6 フレーム加工(改善後) |
続いて実施したPSCモーター、ステーター組付けライン改善は、図1−7を見てほしい。上側が改善前、下側が改善後である。7名から5名へ、2名の少人化に成功した。
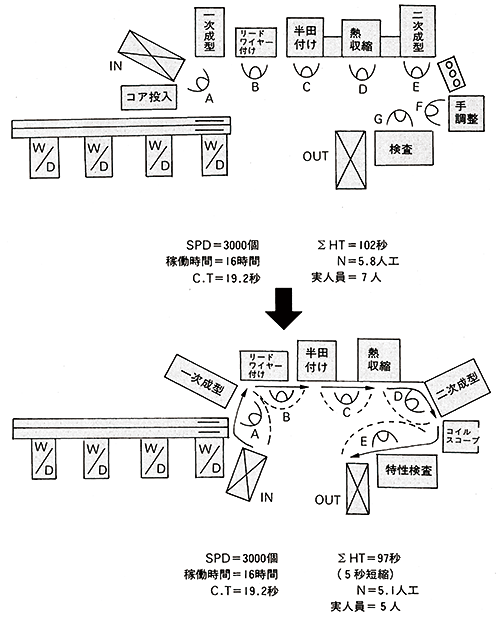 |
図1−7 PSCステーター組付けライン改善 |
- 1)最大のムダは?
改善前の図を見てほしい。理論人員5.8に対し、7名入っている。C.Tが19.2秒であるから、1人当たり約5秒の手待ちが発生していることになる。この手待ちのムダがステーター組付けラインの最大のムダである。原因は人の入れすぎである。
- 2)改善の切り口
改善の切り口は、「手待ち」のムダで切った。ワンマンワン工程持ちから、ワンマン多工程持ちにする。
- 3)即実践
次の改善案を2日間の即実践で実行した。
(1) コアの投入口変更。
(2) 手調整の原因を調べ、調整なしで流せるようにする。
(3) コイルスコープを導入して、分析できるようにする。
(4) 5名の工程設計をし、作業指導書を作成する。
(5) 翌朝、オペレーターにやらせてみる。
- 4)効果
改善の成果は2名少人化、ΣHTは調整のムダをとることによって5秒短縮、効果金額は2名の少人化で年2,200万ウォンである(写真1−3)。
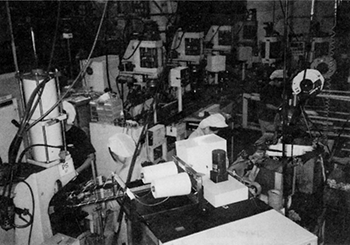 |
写真1−3 PSステーターのUライン |
- <参考文献>
- 1. 工程ばらしのノウハウ 拙著 日刊工業新聞社
- 2. 不良を出さない、つくらない、入れないしくみづくり 拙著 日刊工業新聞社
- 3. 中国に負けない工場 拙著 (株)新技術開発センター
- 4. 工場管理 1994年10月 野口恒氏レポート
- 5. 機械配置改善の技法 新郷重夫著 日刊工業新聞社
- 6. 工場レイアウトの技術 リチャード・ミューサー著 十時昌訳 日本能率協会
- 7. 工場管理(新しいジャスト・イン・タイム生産方式 連載) 拙著 日刊工業新聞社
- 8. 図説ローマ 都市建築の2000年 河辺泰宏氏 河出書房新社
- 9. 儲かる! 1人生産方式 拙著 (株)新技術開発センター
- 10. 進化するトヨタ生産方式 拙著 (株)新技術開発センター
- 当連載は「工場レイアウト改善技術」より。
|