1) |
順送り方式
機械加工におけるU字ライン(製品の投入位置と取出し位置が同じ)づくりの場合は、ワークを右取り・左送りにする場合が多い。その理由は、チャッキングの位置が左側になっている場合が多いためである。
反対に、組立のU字ラインは左取り・右送り方式が多い。これは右手で位置決めする動作が多いからである。
|
2) |
バーナー取付板かしめ工程とプレス工程の連結
要は、図4−1の中央に位置する振分け作業をとってしまい、バーナー取付板かしめ機とプレス機を連結して、図4−2のように1人作業にしてしまうことである。その場合は以下のステップで進めるとよい。
- ① かしめ完了品を左手で取り、プレス上に置いてスイッチを押す。そして、すぐにかしめに行く。
- ② かしめ完了品を右手で取りながら、左手でかしめ機をセットして、右手はスイッチを押しながらかしめ済み品を完了台に置く。
- ③ プレスに移行しながら①に入る。
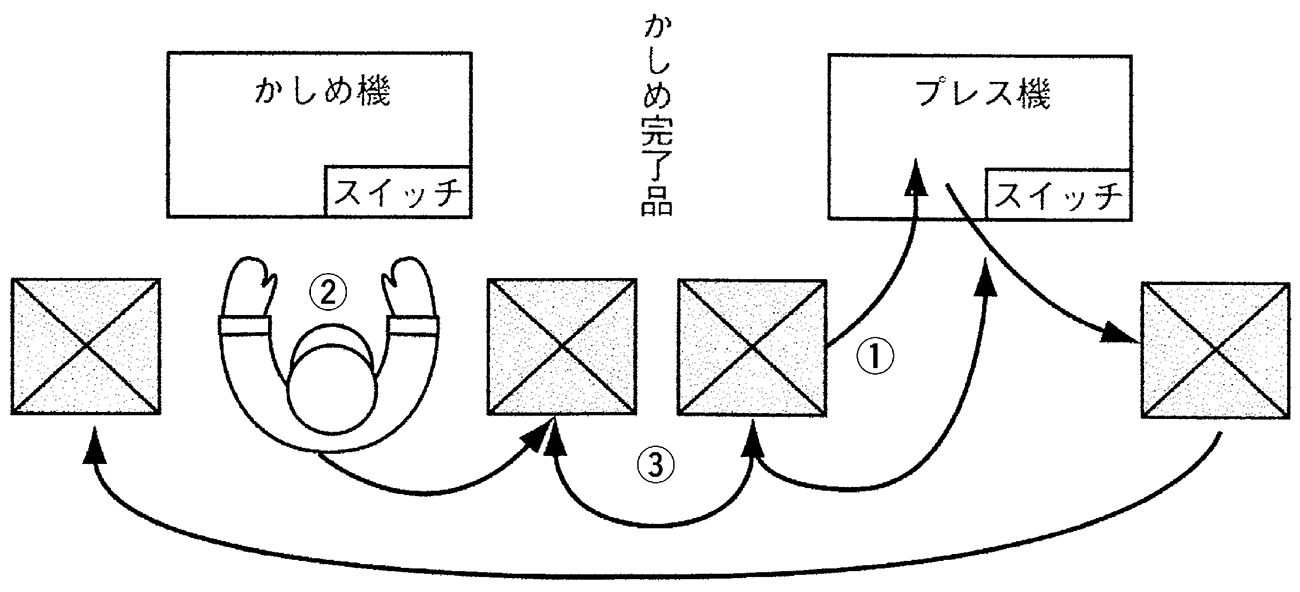 |
図4−2 かしめ、プレスの2台後引き1人作業方式 |
|
3) |
1回目の結果検証
ΣHTは11秒で、目標のサイクルタイムである7秒には残念ながら4秒オーバーした。さらに改善が必要である。「即実践」にはならなかったが、原因は工程間の歩き過ぎである。
|
4) |
異工程連結の工程設計
韓国の平和産業におけるダイカスト工場での機械加工のインライン化では1発で成功した(日刊工業新聞社発行「工場管理」2007年3月号に詳細を掲載)が、今回は1発ではうまくいかなかった。そこで代案であるが、全工程を2ライン直線ラインで工程設計することを提案した。図4−3には、異工程連結の2ラインで1個流しにトライする案を示す。
欠点としては、上板を流すのにコンベヤを用いているため、1個づくりにはならない点である。
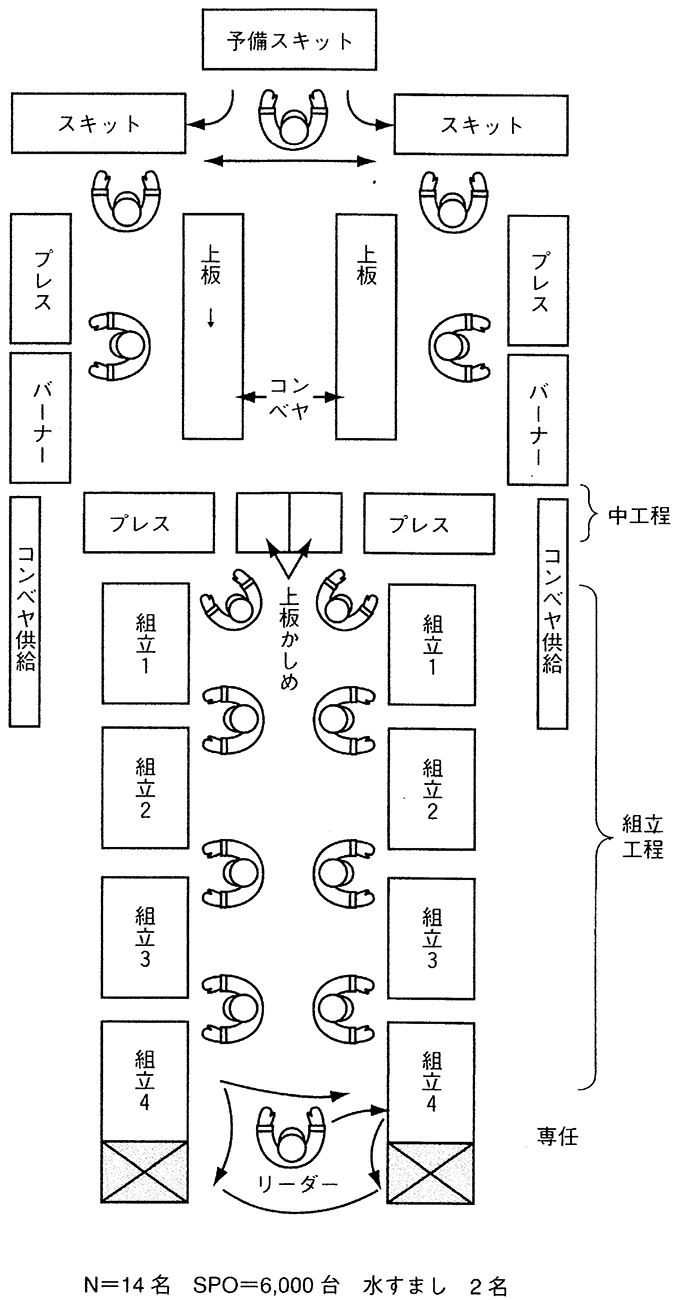 |
図4−3 異工程の連結ライン |
一方の図4−4は二の字ラインで、日産が得意とする工程レイアウトである。ただし上ラインは右取り・左送り、下ラインは左取り・右送りになる。
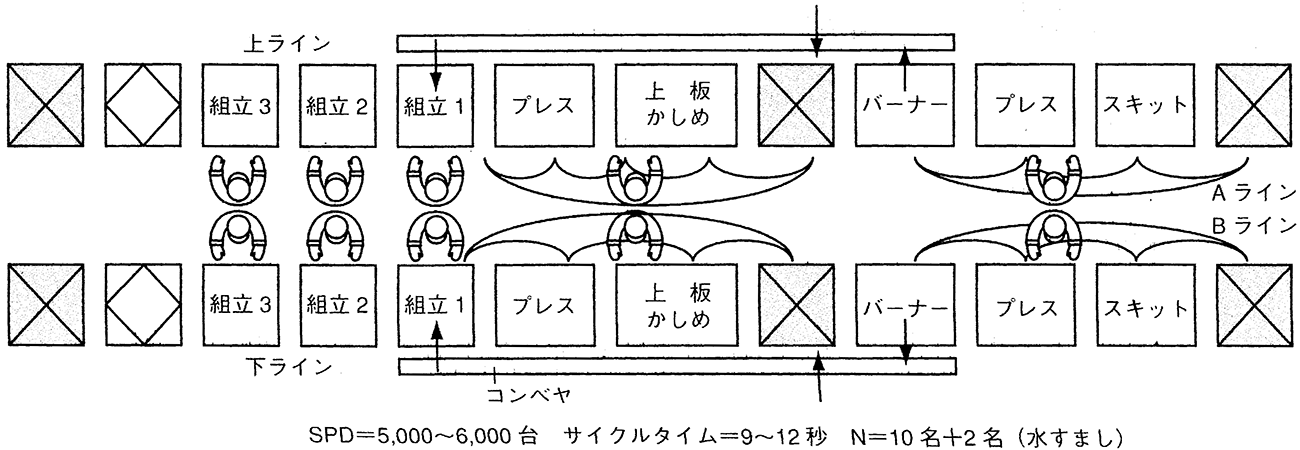 |
図4−4 二の字ライン案 |
|