|
 |
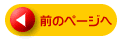 |
1/3 |
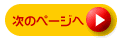 |
不良をつくらないためのツールとして、工程診断表と工程診断要領書を活用し、画期的な成果を上げている企業がある。今回は、「品質保証(QA)部ムダとりマニアル」(編著・関根憲一、定価29,600円)より、フォーマット事例を中心にご紹介いたします。
1.工程診断の実施
たとえば取引先Aの機種グループDのZラインとAラインを比較する。即現場に行き工程別クレーム要因のムダとりを実施する。というのはものづくりのよしあしを工程別に比較するものである。たとえば表1のような診断表を利用するのも一つの方法である。
工程診断を実施する
1)基本的な考え方
クレームがでるのは物づくりの方法(検査方法もふくめ)がわるいから発生するのである。
まず、クレームの多い組立ラインの現場に行く、クレーム品という現物を持って。
クレーム発生の現実を見に行く、実際は見えない(確率的に見て)が、動作のバラツキに注目して物造りのよしあしを分析するのである。というのは品質は工数の影、工数の動作の影であるから、動作のバラツキを工程別に診ていく。
もちろん、現場の責任者にも同道してもらい、個別に診断表を提出させる。手合わせする。
このようにトラブルが発生した都度、現場責任者と現場監督者を実践を通じて教育するのである。
2)初心者の訓練
次のようなチェックポイントについて、訓練コーナーを設け教育する。
- 芯ずれの有無、加工基準不動の原則
- 空中作業
- やりなおし
- リズムくずれ
- 仕掛品、停滞品の有無
- 1個流し、1個組立、1個検査
- チョコテイ、機械故障
- チョイオキの発生
- スクリューの故障
- ねじ、部品のひっかかり
- 後引きになっているか
その他については省略する。
3)うっかりミスはチョイオキでおきる
チョイオキの原因は
- 第1の原因は材料、部品不良の投入
- 第2はラインアンバランス
- 第3はリズムくずれ
- チョイテイ(3分以内の機械トラブル)
チョイテイの原因は生産試作時の工程(ライン)設計不充分であるが、今更いってもはじまらない。
そこで瞬間保全からスタートしよう。
- 瞬間保全法とは
- チョイテイ、メカニズム解析法
4)クレーム要因に対応したライン改善を提案する。
- QCマンが具体策を作成すること。評論家的QCマンは不可。場合により即実践日を決める。
- 即実践とはクレームを出さないための小さな要改善点を発見したら今夜中にとってしまうことをいう。くわしくは「工程ばらしマニアル」(新技術開発センター刊)
2.工程診断要領書
1.目的
この要領は、A社工場生産ラインに於いて、
- クレームの原因除去
- 不良を出さないしくみ作りの確立
を目的として行うライン診断について、具体的実施要領を定める。
2.適用範囲
この要領は、A社工場で生産される製品の製造・検査工程ならびに関連企業及び協力工場にも適用するものとする。
3.工程診断の定義
不適合品の発生・クレームの原因追及及び再発防止を目的とし、行われる工程(ライン)診断をいう。
- 3−1 定期工程診断
- 顧客クレーム集計結果ワースト5について、1回/月行われる工程診断をいう。
- 3−2 特別工程診断
- 重保クレーム・全数不適合品流出クレームなどに対し、臨時に行われる工程診断をいう。
4.診断責任者
- 4−1 工程診断に関する総責任者はA工場長とする。
- (代行者は工場長次長とする。)
- 4−2 工程診断実施責任者は品質管理課長とする。
- (代行者は品質管理担当係長とする。)
5.工程診断の決定
- 5−1 定期工程診断の決定
- (1)品質管理課集計の顧客クレーム集計により、最多発生ラインを工程診断する。
- (2)顧客クレーム集計は、前月分を当月25日までに集計し、翌月5日までに実施する。
- 5−2 特別工程診断の決定
- (1)突発クレーム及び重大なコンプレイント情報があった場合品質管理課長の判断で特別クレームを宣言する。
- (2)特別クレーム発生処理終了後、速やかに工程診断を実施する。
6.工程診断の実施
- 6−1 実施メンバーは下記とし、共同にてライン診断を実施する。
- 品質管理課長 担当製造課長
- 品質管理係長 担当製造係長
- 品質管理担当者 担当製造班長
- 製造技術1Grリーダー
- 製造技術1Gr担当係長
- 製造技術1Gr担当
- 6−2 方法
- 工程をランダムに区分けし、2〜3人チームで各工程の工程診断表にもとづき実施する。
- 6−3 実施メンバーは工程診断書(表1がよいが、ここではB社用の表2を参考として附す)に従い、不良を作らないしくにについて確認を行う。
7.是正処置の即実践及び依頼書の発行
- 7−1 中・軽欠点については工程診断後直ちに改善案を決め、工程診断実施メンバーが即実践に入る。
- 7−2 重欠点と判断されたものについては、即ACTIONを発行する。
8.改善計画書の提出
- 8−1 工場長は、担当部署に対し改善計画書の提出を指示する。
- 8−2 改善計画書の提出は、工場長の指示から3日以内とする。
- 8−3 改善計画書は工場長宛とし、コピーを品質管理課長に配付する。
9.札「品質改善中」の掲示
- 改善計画書提出と同時に、該当ライン先頭に「品質改善中」と書かれた札を掲示する。
10.改善終了の報告
- 10−1 改善担当部署は、各項目毎改善終了の断面で、工場長及び品質管理課長に報告する。
- 10−2 改善計画書に対しやむなく遅れる場合は、事前に工場長、品質管理課長に連絡する。
11.改善内容の確認
- 11−1 改善終了の報告を受けた場合、直ちに再工程診断を実施、内容を確認し、改善計画書にサインをする。
- 11−2 全改善内容が終了した場合、該当ラインに掲示された「品質改善中」の札を外す。
12.改善内容変更
- 改善内容に変更が生じた場合、製造課は品質管理課長へ連絡する。
13.改廃
- この要領書の改廃は、品質管理課長の責任にて実施するものとする。
|