1-1.ヒューマンエラーを防ぐ指導と職場づくり
株式会社SMC 松田 龍太郎 氏
ヒューマンエラーは人に付き物なので付き合い方が大切
ヒューマンエラーの本質は、些細なことの積み重ねで、ちりも積もれば山となる諺通りそのものです。些細なこと故に、気づかない、気にならない、の繰り返しになっていくのです。
でも、茶碗に箸、ご飯に味噌汁と言うように、人にはヒューマンエラーによるミスが付き物であると言うように切っても切れない関係にあります。無理にミスをしないようにしても無理なことで、逆に大きなストレスになります。ミスを前提に付き合うことに発想を変えるのです。ミスを受け入れて付き合い、でもトラブルは避けるのです。たとえば、以下の質問に答えてみましょう。
Q1:左の太陽マークはいくつありますか?
Q2:なぜ数えにくいのでしょうか?
Q3:右側をもっと数えやすくするには、どうしたら良いですか?
工場においても作業ミスなど、ミスの連続ではありませんか?しかし、ミスが発生しても製品を出荷しなければ、トラブルから回避できます。その考え方は、ミスが社内で発生しても、最悪社外に出荷しなければ最悪の事態にならないというものです。いわば、少々のミスがあっても工場内で対処すればトラブルの被害は少ないのです。
でも同じ繰り返しは全くのムダであり、ミスに対して賢く対処していきましょう。これは個人の力では絶対にできません。ピッキング、加工、組立、検査、梱包、出荷の流れ、つまり組織やチームが一体となって顕在化し、ストップをかけることでトラブルの回避可能になります。
さらに、作業環境、作業手順、設備や機械などを整えて、慌てないで標準作業を粛々と生産ができるよう環境整備をします。そうすることで、ミスが発生してもその場で現行犯逮捕のようにミスを明らかにし、さらに真因も解明して再発防止につなげることができます。やがて、きちんと品質つくり込みのPDCAが回り、工程内不良も撲滅できるようになります。
ところが、ハード面の対応方法であるポカヨケ装置の開発や設置だけでは、ミスをゼロにはできません。多くの工場ではハード面を整備することで、ミスをなくせるとハード面の整備や充実に目を向けておられます。人間も体だけでなく、技術や心も充実と合わせて、心技体と言う三位一体のバランスの取れた状態を維持し継続することが大切です。
同様にハード面だけでなく、使う側や提供する側の考え、つまりソフトが重要になります。なぜやるのか、やらないとどうなるのか、もっと楽にもっとわかりやすくなどのソフト面もセットにしていくことも大切です。
ミスが激減する5つのポイントとは?
①安全で働きやすい職場づくりです。モノが多いと探しのムダが発生しますが、その割合は就業時間の約3割を占めているのです。ですから職場の仕掛を減らすことがカイゼンになります。モノが少ないと探しのムダがなくなります。ちょっとしたことで、慌てないからミスも少なくなり生産性も向上します。
②作業環境の整備の考え方です。治工具や部品を手元に並べ工具と部品を順番に並べることで、作業性が一気に良くなりミスも激減します。そのためにも、現場の仕掛を区分して最小限にします。そして、工程結合してスムースな流れを構築します。
③社員を安全活動に巻き込むことです。安全が確保できないと、社員は身の安全をとても気にしながら作業をしなければなりません。作業性や品質面で大きなブレーキになります。安全が確実に確保できれば、生産性や品質向上さらには職場の雰囲気も良くなります。安全教育は、重要な教育投資なのです。でも理解していない経営トップが多くいます。社員を巻き込み、自ら職場を整備させなければなりません。
禁煙マークは、AとBのどちらが正しいか、
なぜですか、答えられますか?
皆さんの答えは、A=2割、B=8割です。
さて正解は?
本文の最後に正解が掲載されています
④安全の確保が品質や生産性を向上させます。③と同様に人は自分の身の安全が担保されていないと、社員は作業に集中できません。自分の身は自分で守る意識を植え付けて自ら身を守ることができれば、現場の自律化やチーム意識を向上できます。
⑤フィロソフィ(思想・哲学)を共有化します。これは、一見見えないものですし気にもならないものですが、もっとも大切だと考えます。まるで空気のような存在です。人は何のために働くのか、人は何のために生まれたのか、企業や会社は何のために存在するのか。そして、その使命は何かなど基本を納得し腹に据えることで、一人ひとりが自ら考え、自ら考動し、自らの価値を上げる人や育成していく人につなげていきます。
これがなければ、仕事=作業になってしまい、何も考えない人に陥ってしまいます。実にもったいないことです。仕事=作業+改善(付加価値をつける)ことを、毎日当たり前にして、常に自ら向上し組織としてもスパイラルアップを目指すことが大切なのです。
チームをまとめるリーダーの存在とその行動とは?
職場は、単なる製品を生産するだけの存在で良いでしょうか。当然ダメですね。人が集まっているだけの何らかのグループ(烏合の衆らしきもの)と、志をもったチームとは全く違いがあります。チームには、チームリーダーが存在します。あるべき方向に導いていくリーダーがいるかいないかで、その組織は全く違った存在になります。それを例えると、頭がある人間と頭のない動物の違いです。
リーダーを一言で言えば、奉仕者やボランティアです。率先垂範ができ、自己中心でなく人のためにすぐに行動し働ける人です。リーダーは、肩書や地位ではなく、心構えや姿勢をどう捉えるかの問題です。一回限りの片道切符をもった人生を、どう完全燃焼して世のため人のために活かすか、まあええかと不完全燃焼の一酸化中毒状態の人生で過ごすか。さあ皆さんはどうしますか?
姿は人間だが単なる動物のように生きるか、それとも霊長類最高の人として全うするような人生として生きるのか。志一つで、あなたの行動は変えることができます。
ヒューマンエラーを何度も繰り返すことは、自分の人生だけではなく、家庭や職場や組織までも影響を及ぼします。一つでもミスをなくす取組みと再発防止策、さらには未然防止までも行い、ミスによる損失を激減させましょう。そして、ミスをなくして儲かる組織に変えていきましょう。
答えは、Aが正解です。NOのNのスラッシュ(\)がOに移動したからです。
※「ヒューマンエラー」を詳しく解説するセミナーを開催いたします
1-2.バス置き去り事故の再発 (しくみに落とし込んでも、違うかたちで再発する!)
株式会社 遠藤メソッド 遠藤 友貴哉 氏
2024年6月13日(NHK WEBニュース)「通園バス 置き去り防ぐ安全装置 設置後に降ろし忘れが なぜ?」という題名で、バス置き去りの再発がニュースになりました。
園児をバスから降ろし忘れただけで命に別条はなく、大きな問題にならなかったのは幸いでした。このバスには安全装置が取り付けられていますが「バスの置き去り」は発生しました。しくみで解決しても、違う形(事象)で再発するのです。やっぱりと言っていいのか、残念でなりませんが、正しい再発防止策が実施されていないので、当然と言えば当然の結果とも言えます。
<記事一部抜粋>
後ろから2番目の席の窓際に座っていた4歳の男の子は、前の席に隠れる形で眠っていて、まだ降りていませんでした。添乗の職員は前方から園児が残っていないかを目視で確認しましたが、その位置からは男の子は死角になっていました。降車時にチェック表で人数の確認も十分に行われなかったため、降ろし忘れていることに気が付くことができませんでした。運転手や添乗の職員は別の送迎ルートに出発し、15分ほどたってから園児を降ろし忘れていたことに気がつきました。車内は冷房がかかっていたため園児の体調などに問題はなかったということです。
安全装置は、静岡県牧之原市の認定こども園での事件で設置が義務化されたもので、この園では前の月に設置したばかりでした。ただ、エンジンを切らないと警報音は鳴らない仕組みだったため、安全装置は作動しませんでした。
この園でも対策は打たれていますが、どれも「しくみ」の対策です。この園が悪いわけではありません。こういった「しくみ」の対策を取らないと、さまざまなところからの指摘がなくならないからです。
ハインリッヒの法則に当てはめて考えてみると、死亡事故(重大事故:1)には至っていませんが、「園児バス置き去り」のトラブル(軽微な事故:29)は減っていません。現場には、ヒヤリハット(不安全行動)が発生していることになります。(ヒヤリハット:300)そのヒヤリハットの原因である「不安全行動:9・不安全状態:1」は「後ろから前まですべての席を覗き込み目線を当てていない、園児がいないことを判断していない」見てない不安全行動です。添乗員が確認するときは「後ろから前まですべての席を覗き込み目線を当てて、園児がいないことを判断する。」このことを習慣(体が覚える)になるように訓練しなければ、事故の再発防止は出来ません。
安全装置も、使い方・設定・調整・メンテナンスを間違えば、正しく動作しません。
これは人的ミス(ヒューマンエラー・ポカミスなど)の問題です。
一般的な見方では、エンジンを切って車庫に入れる際には、安全装置がエンジン停止後に警報音を鳴らし運転手に車内の確認を促すので、大丈夫だろうと考えますが、ハインリッヒの法則で言えば、(ヒヤリハット:300)ではなく、(軽微な事故:29)が発生しています。言わばたまたま死亡事故にはならなかっただけです。「園児がいないことを判断する。」ことが習慣になっていないのであれば、安全装置の使い方・設定・調整・メンテナンスで、何らかの「見ていない」が重なれば、事故は再発します。ダブルチェックよりトリプルチェックの方が、理論的には検出率がアップしますが、実際の検出率は下がる理屈と同じです。(前の人が確認しているから大丈夫だろう。)また、手順で指導しても判断は形骸化し「見ていない」「見られない」は発生します。
このたび発生した園児のバス置き去り事故の対策は、しくみ(決めごとなど)・運用(管理の問題)・土壌(意識の問題)と、様々な観点で、発生防止と流出防止など、ロバスト性(堅牢性・頑健性)を考えないといけませんが、そもそもこの事故が発生したのは、意識して見るべきところ見る習慣がないことです。また、何か気になることがあったり、声をかけられたり、急いでいたりして、本人は見ているつもりですが、図「バス降車時の目視確認」のようなノウハウを実行していなかった瞬間があって「見ていない」が発生したということです。しかし、失敗しないベテランと呼ばれる達人のような人は、何か気になることがあったり、声をかけられたり、急いでいたりしても、図「バス降車時の目視確認」のようなノウハウを実行してから、次の作業に移ります。
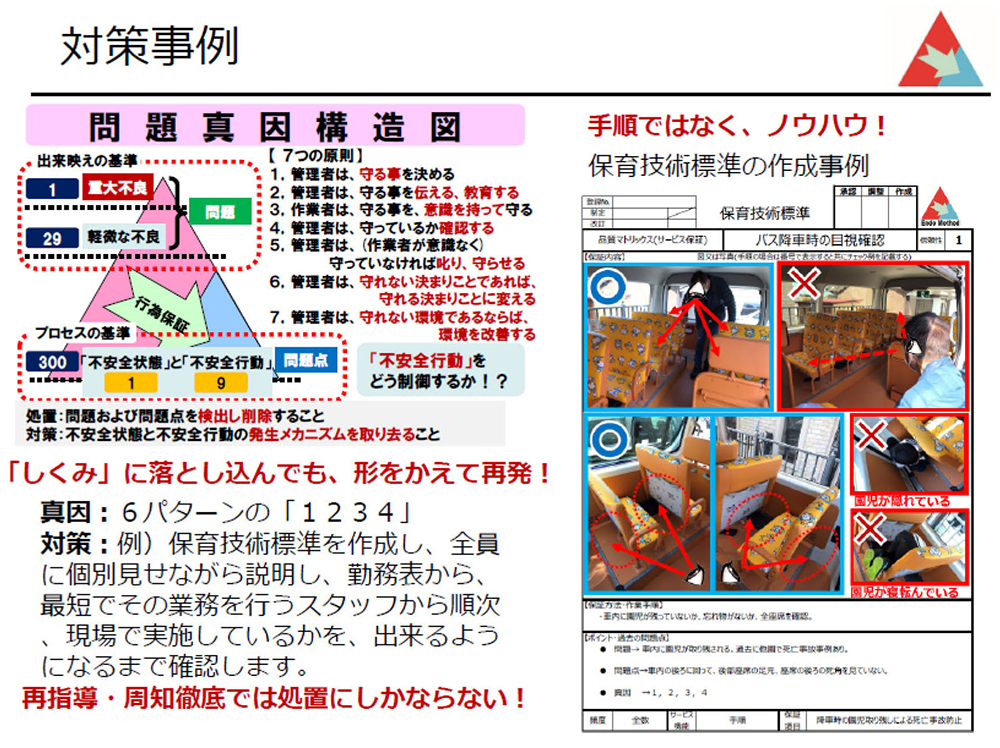
図「バス降車時の目視確認」
失敗したことがある経験者は、二度と失敗しないために気づいたこと「絶対しなければならないこと」「絶対してはならないこと」を明確にし、考えなくても反応できるように、体に覚えさせます。(くせ・習慣・無職の意識化)見る(診る・判断する)ことを習慣にすることで、必ず見るべきところ見るようになり、必ず不具合に反応出来るようになります。これが、失敗しないベテランと呼ばれる達人のような人がやっていることです。事故やクレーム、品質不良などの不具合を対策するには、まずは「ちゃんとした仕事・作業」の中身を具体的にすることです。「ちゃんと」にノウハウが隠れています。ノウハウは、こんなことぐらいで失敗しないことです。「行為保証2.0」では、ノウハウが誰でもわかる技術標準という書き方がありますが、まずはノウハウを明確にすることが重要です。
そして「運用」では、問題を解決するには、管理者が行っている管理(やり方)を変えなければ対策にはなりません。「指導」や「周知徹底」という言葉で丸められることがほとんどですが、実際は、管理者の伝え方が悪かったり、守っているか確認していなかったり、管理の悪さが問題になっていない状態では、運用の問題は解決できません。
「土壌」は、意識です。「しくみ」と「運用」が確立することで、管理者や作業者など当事者の意識が高まっていきます。この意識が、決まり事を守る力となり、守るのが当たり前の感覚が定着します。
お伺いするさまざまな現場で、作業者指導を行っていますが、その多くは、教育だけで、訓練まで行っていません。ルールを守るのは当たり前ですが、実際にルールを守るのは、訓練や練習をしないと守れないものです。守れる人からすると簡単なことのように感じますが、みんなが守る状況を創り出すのは、実は難しいことなのです。人は理解したり、気づいたりするだけで、出来たりしないものです。出来るようにするためには、必ず訓練(練習)が必要です。
よくある対策で、安全や品質で、注意喚起を行う研修やセミナー、ポスター掲示、回覧など行いますが、意識を上げることが出来たとしても、それは記憶ですので、必ず忘れてしまいます。しなければならないのは、その高い意識の先にある「習慣にする」ということです。ここまでやってはじめて「管理している」「指導している」と言えます。
「行為保証2.0」は、製造業やサービス業などさまざまな現場で、人の判断や行動基準に作業の精度を管理する手法として、体系化し、理論構築された取り組み・活動です。一般的に「ヒューマンエラー」は、ゼロにすることはできないと考えられていますが「行為保証2.0」は「見えない」「見ていない」「見られない」を管理することで、 この問題を解決する1つの解(答え)になります。
「行為保証」である、必ず見る(判断する)ことを、考えなくても体が勝手に見てしまう習慣になるよう訓練すれば、ヒヤリハット(不安全状態・不安全行動)の「見てない」「見られない」をゼロにすることが出来、事故は発生しません。行為保証の取り組みでは、多くの成功事例があり、結果(エビデンス)が出ています。現在の出来栄え管理でしくみや手順で対策しても、行為保証といった観点視点でアプローチしなければ、結局は、形を変えて再発してしまうだけです。こういった事故が一日でも早くなくなること願うばかりです。
※「行為保証」や「技術標準」を詳しく解説するセミナーを開催いたします
1-3.ポカヨケの秘訣
ポカヨケとは
ポカヨケとは、もともと米国からフール・プルーフシステムとして航空機のものづくりの技術として導入されたものである。フール・プルーフシステムを直訳すると馬鹿防止システムつまり、バカヨケということになり、誰が作業をしても間違えないように出来る作業システムのことを指しているのだが、日本では人聞きが悪いのでポカヨケと一般に呼称されるようになった。
ポカヨケは、ポカミスの発生を予見し、あるいは、検知しその予防、あるいは、防止の対策をさして言う言葉である。ポカミスそのものを指す言葉には、他にも「凡ミス」「うっかりミス」「ケアレス(不注意)ミス」「ぼんやりミス」などと呼ばれるものがある。
ポカミスの原因
ポカヨケの意味は、上で述べたとおりであるが、ポカヨケをしなければならないのは、ポカミスが発生するからである。その原因としては、仕事をしている間中、人はミスをしないように注意を集中し続けることが出来ない点にある。
なぜ、注意を持続できないか?
それには、色々な要因があるが、結論を言えば人の持つ人間的特性そのものと考えられる。いずれにしても、人に仕事を頼んで、そのままにしておくといつか必ずミスを犯すと考えたほうがよい。ポカミスによる不具合のデータを出せといったらどこの企業でも枚挙にいとまがないくらいに出てくるだろう。人間だからミスを犯す。従って、すべての仕事にミスはつきものであるから仕方がないとしておけば、ミスによる経営的な損失は、膨大なものになるだろう。
ここに、ポカヨケ・システムの重要性が問われることになる。ミスは誰でも犯すといっても、同じ人間の間でも、ポカミスを起こす頻度に差があることも事実である。ほとんどミスを犯さないという人もいれば、始終ミスを犯す人もいる。ポカミスに関しては、人の間にばらつきがあるということもデータで確認されている。
では、いったい人はどのような状況になったときにミスが増えるのだろうか。このメカニズムが明確になれば、ポカヨケ対策がしやすくなるはずである。
ポカミス発生のメカニズム
ポカミスは人為的ミスであるから、属人的な要因により発生する。従って、ポカミス発生の予防は、人の使い方、人への働きかけを適正に行うことが基本となる。このことは、取りも直さずマネジメントの基本にも通じることである。具体的には「男女間の特質」、「人間性格」、「疲労」、「注意力」、「仕事の単調感」、「仕事の環境」などの視点からポカミス発生のメカニズムを理解し、適切な対策を打つことが有効である。
※詳細は、「ポカヨケの秘訣① 基礎編」で解説している。
ポカヨケの狙い
品質管理の本質は、工程で造り出される製品(物とかソフト、サービスなど)の不良をできる限り減らして、最終的には無くしてしまうための一つの活動である。その方法は、「管理」であるから「予め計画をして、不良を発生する原因を事前に取り除いて仕事に取りかかる」ということである。それを具体的な方法を使い、実際に実行することによって具体的な成果が上がっている。その中に「ポカヨケ」と呼ばれる物がある。「ポカヨケ」の狙いは「ヒューマン・エラーを防ぐ」ということである。
ヒューマン・エラーとは何か?
「ヒューマン・エラーとは何か」を一言で言い切るのは難しいが、言葉の上で出てくる「ウッカリミス」。これは、言われたことを聞き逃したり落としたりとか、友人とすれ違っているのに、自分は友人と会っているということが分からないというようなことである。時に「あ〜、ウッカリしていました」と言うことである。
もう一つよく言われるのは、「ボンヤリミス」である。いわゆる「頭がボーとしていて」赤信号を何故か知らないが渡ってしまい、何かおかしいと気付いて後ろを見ると誰も歩いていないことを知り且つ赤信号であることを知り慄然とする。どうして自分が赤信号なのに強引に渡ってしまったのかよく分からない。
このようなことを「ヒューマン・エラー」というわけであるが、そうだとしてもやはり「どうしてそのようなことが起こったのか」ということは、極めて主観的で、本人にしか本当のことは分からないので、本人に理由や原因を言ってもらう必要かある。これがまた難しいことなのである。
しかし、このまま放っておくわけにはいかないので、何か対策することになる。そうすると何か理屈をたてる或いは実際にそのことが起きたところを見るというようにして、対策を立てていくことになるのである。従って「ヒューマン・エラー」の対策でも、「起こった瞬間にその場所で現象を捕まえて対策をしていく」という現場での行動やその時点での対応が大切なのである。
ヒューマンエラー対策
改善という面で考えると、ヒューマン・エラーにとどまらず「三現主義」が大切で、例えば「現場へ行ってじっと見ていなさい」ということになる。しかし、現場で「看ていて」分かるには、生産技術とかヒューマン・エラーの知識や行われている活動を解釈しながら観察できるような技能が必要で、ただ単に「見ている」だけでは目的は果たせない。ヒューマン・エラーの実例のみを学ぶだけでは、実戦への応用面でいつかは行き詰まる。ヒューマン・エラーの発生のメカニズムと実戦での具体化がどういう形で結びついて、どういうポカヨケになったのかをよく理解しなくてはならない。「ヒューマン・エラーとはどんなものか」を理屈として知り、次に「ヒューマン・エラーに対する対策をどのように考えていくか」を理解する。最後に「ポカヨケ」とか「品質管理の中でヒューマン・エラー対策をどう取り入れていくのか」「現場改善グループとかQCサークルの大切さや職制の役目」、品質管理で最も大切な「再発防止ということの正しい考え方」を理解する。
※詳細は、「ポカヨケの秘訣② 実践編」で解説している。
|